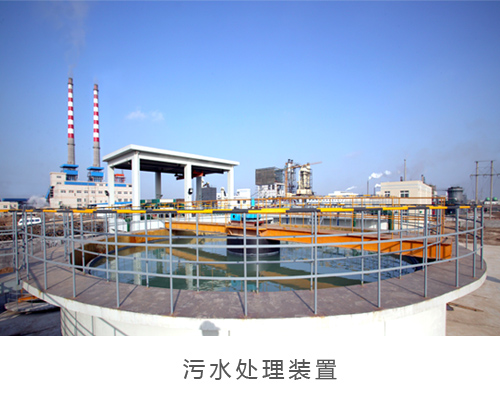
As a responsible listed company, Yaxing Chemical is willing to take on social responsibility and attaches great importance to environmental protection. The company passed the ISO14001:2004 environmental management system certification in 2008 and the clean production audit in 2011.
Yaxing Chemical builds its product chain according to the circular economy model. The caustic soda produced is used to prepare hydrazine hydrate, which is then used to prepare ADC foaming agent. The by-product ammonia water of ADC foaming agent is reused for hydrazine hydrate production and thermal flue gas denitrification. The chlorine gas produced from caustic soda production is used to prepare CPE, and the hydrogen gas discharged is used to process hydrogen peroxide, which can be used to treat industrial wastewater. Through this circular economy model, the balance of chlor alkali and the circular connection between new and old industries are achieved, achieving the unity of environmental, social, and economic benefits.
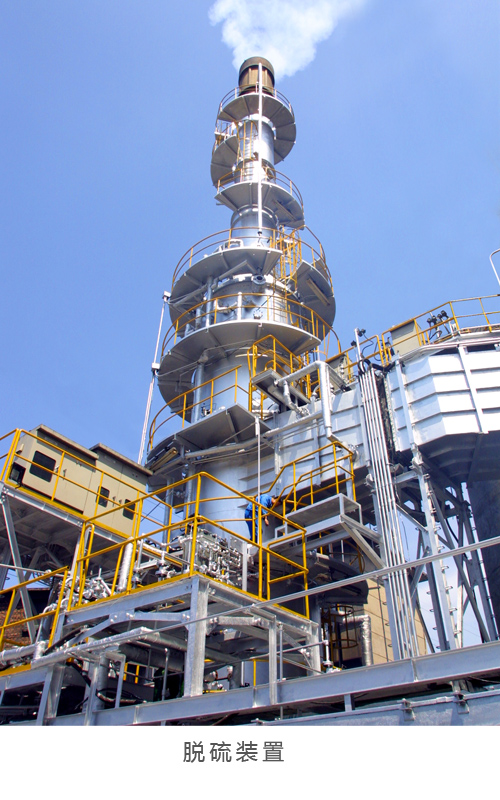
Yaxing Chemical insists on using new technologies and equipment for pollution control. In 1995, the first batch of wet flue gas desulfurization devices for boilers in China were built using advanced technology and equipment from Mitsubishi Heavy Industries, Japan. The desulfurization rate reached over 85%, and it was recognized by the National Development and Reform Commission as the first industrial boiler built in China and one of the best demonstration devices for desulfurization effect; In 2009, Yaxing Chemical Thermal Power Branch adopted first-class equipment and DCS control system to build a desulfurization device, which achieved online monitoring and remote data transmission. The desulfurization rate can reach 95%, and the sulfur dioxide emission concentration in the treated flue gas can be controlled below 200 mg/m3; In 2013 and 2014, the company invested 22 million yuan in the construction of desulfurization, denitrification, and dust removal technology renovation projects for two consecutive years. The renovated desulfurization device adopts a combined process of calcium injection inside the furnace and wet flue gas desulfurization outside the furnace for flue gas desulfurization, with a stable desulfurization efficiency of over 95% and an annual reduction of sulfur dioxide emissions of more than 5300 tons; The newly built denitrification device based on the boiler operating conditions and site conditions adopts the SNCR process, using the by-product ammonia water from the company's foaming agent branch as the denitrification agent, with an efficiency of 70% and a low ammonia escape rate. The concentration of nitrogen oxides emitted is significantly lower than the environmental standards; The renovated dust removal adopts a multi-stage combination electrostatic dust removal patent and a new material bag dust removal process, with smoke and dust emission concentrations lower than environmental standards.
In 2015, the company will continue to increase investment in environmental protection, plan to build a new set of desulfurization absorption tower, and carry out deep dust removal transformation on the flue gas dust removal devices of boilers 1 and 2, in order to meet the stricter emission standards ahead of schedule.